Custom plastic extrusion tailored to your industry needs
Custom plastic extrusion tailored to your industry needs
Blog Article
A Comprehensive Overview to the Process and Benefits of Plastic Extrusion
In the large realm of manufacturing, plastic extrusion becomes a very efficient and crucial procedure. Translating raw plastic into continuous accounts, it accommodates a plethora of markets with its exceptional convenience. This guide aims to illuminate the intricate steps associated with this method, the sorts of plastic appropriate for extrusion, and the game-changing benefits it gives the industry. The taking place conversation assures to unfold the real-world effects of this transformative process.
Comprehending the Basics of Plastic Extrusion
While it may appear complicated in the beginning glimpse, the process of plastic extrusion is fundamentally straightforward - plastic extrusion. It is a high-volume production technique in which raw plastic is thawed and shaped right into a continuous account. The procedure starts with the feeding of plastic product, in the kind of powders, granules, or pellets, right into a warmed barrel. The plastic is after that thawed utilizing a combination of warm and shear, applied by a turning screw. When the molten plastic gets to the end of the barrel, it is required with a little opening referred to as a die, forming it into a preferred kind. The shaped plastic is then cooled down, solidified, and reduced into wanted lengths, completing the procedure.
The Technical Process of Plastic Extrusion Explained

Sorts Of Plastic Suitable for Extrusion
The option of the ideal type of plastic is an essential aspect of the extrusion procedure. Various plastics offer one-of-a-kind homes, making them much more matched to certain applications. Polyethylene, as an example, is generally used due to its affordable and very easy formability. It uses outstanding resistance to chemicals and dampness, making it excellent for items like tubing and containers. Likewise, polypropylene is another prominent option because of its high melting factor and resistance to tiredness. For even more durable applications, polystyrene and PVC (polyvinyl chloride) are commonly selected for their stamina and resilience. These are typical options, the selection ultimately depends on the specific demands of the product being generated. Recognizing these plastic kinds can substantially improve the extrusion procedure.
Contrasting Plastic Extrusion to Various Other Plastic Forming Approaches
Recognizing the kinds of plastic ideal for extrusion paves the way for a broader conversation on how plastic extrusion piles up versus other plastic creating techniques. Plastic extrusion is unrivaled when it comes to creating constant profiles, such as gaskets, seals, and pipes. It additionally enables for a consistent cross-section along the length of the product.
Key Advantages of Plastic Extrusion in Production
In the world of manufacturing, plastic extrusion offers lots of significant advantages. One notable advantage is the cost-effectiveness of the process, which makes it a financially attractive production technique. Furthermore, this method offers premium product adaptability and boosted manufacturing speed, therefore enhancing general production efficiency.
Affordable Production Method
Plastic extrusion leaps to the forefront as an affordable manufacturing approach in manufacturing. This procedure sticks out for its capacity to produce high volumes of material swiftly and successfully, providing producers with significant financial savings. The primary expense benefit is the ability to utilize cheaper resources. Extrusion uses polycarbonate products, which are less expensive contrasted to ceramics or metals. Additionally, the extrusion process itself is reasonably simple, minimizing useful source labor expenses. Additionally, plastic extrusion calls for much less power than traditional production techniques, adding to lower functional costs. The procedure additionally minimizes waste, as any malfunctioning or excess materials can be reused and reused, offering an additional layer of cost-effectiveness. Overall, the economic advantages make plastic extrusion an extremely attractive alternative in the manufacturing industry.
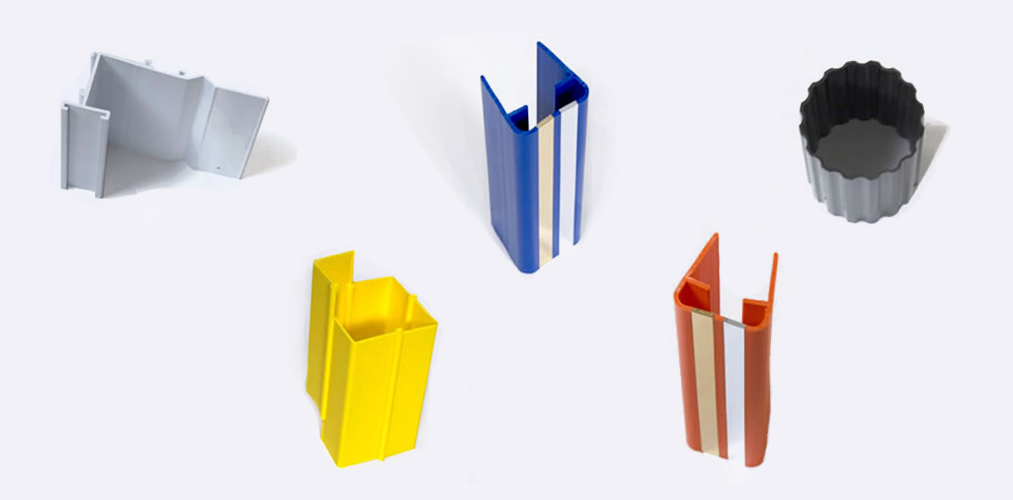
Superior Product Adaptability
Beyond the cost-effectiveness of plastic extrusion, an additional significant advantage in making lies in its superior item versatility. This process enables the creation of a wide range of items with differing designs, sizes, and shapes, from simple plastic sheets to detailed profiles. The flexibility is credited to the extrusion pass away, which can be personalized to produce the wanted product design. This makes plastic extrusion an optimal solution for industries that call for tailored plastic elements, such as vehicle, construction, and packaging. The ability to generate varied items is not just beneficial in meeting certain market needs however additionally in enabling suppliers to explore brand-new product with marginal capital expense. Fundamentally, plastic extrusion's item flexibility promotes advancement while boosting operational performance.
Improved Production Rate
A substantial benefit of plastic extrusion hinges on its improved production rate. This production process enables for high-volume production in a fairly official statement brief time period. It is capable of producing long, constant plastic profiles, which significantly minimizes the production time. This high-speed production is specifically advantageous in industries where big amounts of plastic parts are required within tight deadlines. Couple of other manufacturing processes can match the speed of plastic extrusion. Furthermore, the capability to maintain consistent high-speed production without compromising item top quality sets plastic extrusion apart from various other methods. The enhanced production speed, therefore, not just enables suppliers to meet high-demand orders however likewise adds to raised efficiency and cost-effectiveness. This useful attribute of plastic extrusion has made it a favored choice in various industries.
Real-world Applications and Influences of Plastic Extrusion
In the realm of manufacturing, the strategy of plastic extrusion holds extensive significance. The financial advantage of plastic extrusion, go now mainly its high-volume and affordable outcome, has actually reinvented manufacturing. The industry is persistently making every effort for advancements in eco-friendly and recyclable materials, showing a future where the advantages of plastic extrusion can be retained without endangering environmental sustainability.
Verdict
To conclude, plastic extrusion is a highly efficient and effective method of transforming resources into varied items. It provides countless advantages over various other plastic forming techniques, including cost-effectiveness, high outcome, marginal waste, and layout flexibility. Its influence is profoundly felt in different industries such as building and construction, automobile, and consumer products, making it an essential procedure in today's manufacturing landscape.
Diving much deeper into the technological process of plastic extrusion, it starts with the option of the suitable plastic material. When cooled, the plastic is reduced right into the needed lengths or injury onto reels if the item is a plastic movie or sheet - plastic extrusion. Comparing Plastic Extrusion to Various Other Plastic Forming Approaches
Understanding the kinds of plastic ideal for extrusion paves the means for a more comprehensive discussion on exactly how plastic extrusion stacks up against various other plastic creating methods. Couple of other production processes can match the rate of plastic extrusion.
Report this page