High-performance plastic extrusion solutions for manufacturers
High-performance plastic extrusion solutions for manufacturers
Blog Article
Key Advantages and Considerations of Executing Plastic Extrusion in Your Tasks
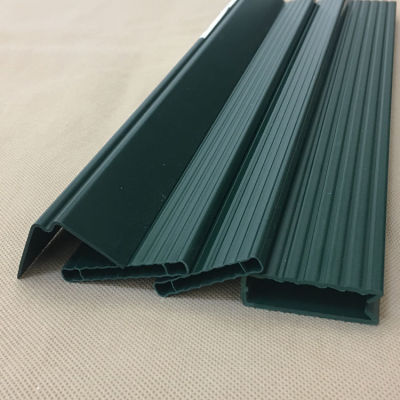
Comprehending the Basics of Plastic Extrusion
Plastic extrusion, a staple in the production market, is a process that involves melting raw plastic product and reshaping it into a constant profile. This account, as soon as cooled down, can be cut into wanted lengths or curled for later usage. The appeal of plastic extrusion depends on its flexibility. A wide range of items, from piping to home window frames, can be produced. The procedure calls for an extruder, a complex machine with a heated barrel, a revolving screw, and a die at the end. The plastic product, in the type of pellets, is fed right into the extruder, where it's melted and forced via the die, taking its form. The choice of plastic and the style of the die determine the item's features.

The Economic Benefit of Plastic Extrusion
The financial benefit of plastic extrusion lies primarily in 2 areas: cost-efficient material production and advantageous manufacturing speeds. With plastic extrusion, services can produce high quantities of product at a reduced cost compared to various other approaches. The procedure flaunts an impressive production rate, considerably lowering time and more enhancing its financial viability.
Cost-efficient Material Production
A substantial benefit of plastic extrusion is its exceptional cost-effectiveness. This production procedure enables continuous, high-volume production with very little waste, which equates right into reduced expenses. The raw materials utilized, typically plastic pellets, are relatively economical contrasted to other compounds (plastic extrusion). The process itself needs less energy than lots of other manufacturing approaches, further decreasing prices. In addition, the extrusion procedure enables for a high degree of accuracy fit the plastic, reducing the demand for pricey post-production changes or modifications. The durability and longevity of extruded plastic products typically imply less require for substitutes, contributing to long-lasting savings. All these factors make plastic extrusion a very cost-effective choice for lots of jobs, offering an eye-catching balance between cost and efficiency.
Beneficial Manufacturing Speeds
While maintaining the cost-effectiveness of the products, one more significant advantage of plastic extrusion depends on its quick production rates. This performance in the manufacturing process is connected to the constant nature of the extrusion process, enabling for high-volume manufacturing in a fairly short time span. The speed of production directly associates to a decrease in labor expenses and a boost in result, thus boosting the overall financial viability of the process. In addition, the fast-paced manufacturing does not jeopardize the top quality of the final product, making certain constant and reputable results. This combination of speed, cost-effectiveness, and high quality underscores the significant economic advantage of carrying out plastic extrusion in different tasks.
Flexibility and Personalization: The Strengths of Plastic Extrusion
Among the noticeable strengths of plastic extrusion depends on its flexibility and customization possibility. These top qualities unlock to limitless design opportunities, providing producers the capacity to customize products to details demands. This increased level of modification not only boosts product performance but also considerably increases item uniqueness.
Limitless Layout Opportunities
Plastic extrusion radiates in its ability to supply nearly limitless layout possibilities. This approach gives flexibility to develop complex profiles and complicated forms, an accomplishment tough to accomplish with various other fabrication strategies. Owing to the fluid nature of liquified plastic, the process is versatile enough to yield a varied array of dimensions, forms, and dimensions. The plastic can be manipulated to match one-of-a-kind Discover More specifications, permitting the production of tailored geometries and meeting particular customer demands. Plastic extrusion can manage a selection of plastic kinds, increasing its application range. This versatile strategy, as a result, offers a wide variety of sectors from construction to vehicle, product packaging to electronics, and past. With plastic extrusion, the layout possibilities are practically limitless.
Improving Item Individuality
The adaptability of plastic extrusion can considerably boost item uniqueness. This process enables designers to explore different shapes, sizes, and shades, providing them the flexibility to produce distinct items that attract attention on the market. It is this customization that lends a distinctive identification per item, differentiating it from its competitors.
In addition to its visual advantages, the customizability of plastic extrusion likewise uses practical advantages. Thus, plastic extrusion not just enhances item individuality however additionally its utility and bankability.
Style Limitations in Plastic Extrusion: What You Required to Know
How can make limitations potentially affect the process of plastic extrusion? While plastic extrusion is functional, design constraints can cut its advantages. Particular complex styles might not be practical because of the restrictions of the extrusion procedure, potentially restricting the production of complex accounts. The process is less appropriate for multi-chambered or hollow frameworks. In addition, the extrusion process may not always offer the preferred surface coating, specifically for those requiring high gloss or optical clearness. Material choice more helpful hints can likewise posture challenges, as not all polymers are suitable for extrusion. High-temperature immune plastics, for example, may present problems. Comprehending these constraints is critical for reliable implementation of plastic extrusion in your tasks. plastic extrusion.
Evaluating the Environmental Impact of Plastic Extrusion
While recognizing style constraints is a significant facet of plastic extrusion, it is just as important to consider its ecological implications. The process of plastic extrusion involves melting plastic materials, potentially releasing damaging gases into the setting. Better, the resulting items are often non-biodegradable, adding to garbage dump waste. Developments in modern technology have actually enabled for even more environmentally-friendly practices. Making use of recycled plastic products in the extrusion process can lower environmental effect. Additionally, establishing naturally degradable plastic options can help alleviate waste problems. Reviewing these ecological aspects is essential when carrying out plastic extrusion tasks, ensuring a balance between efficiency, cost-effectiveness, and environmental obligation.
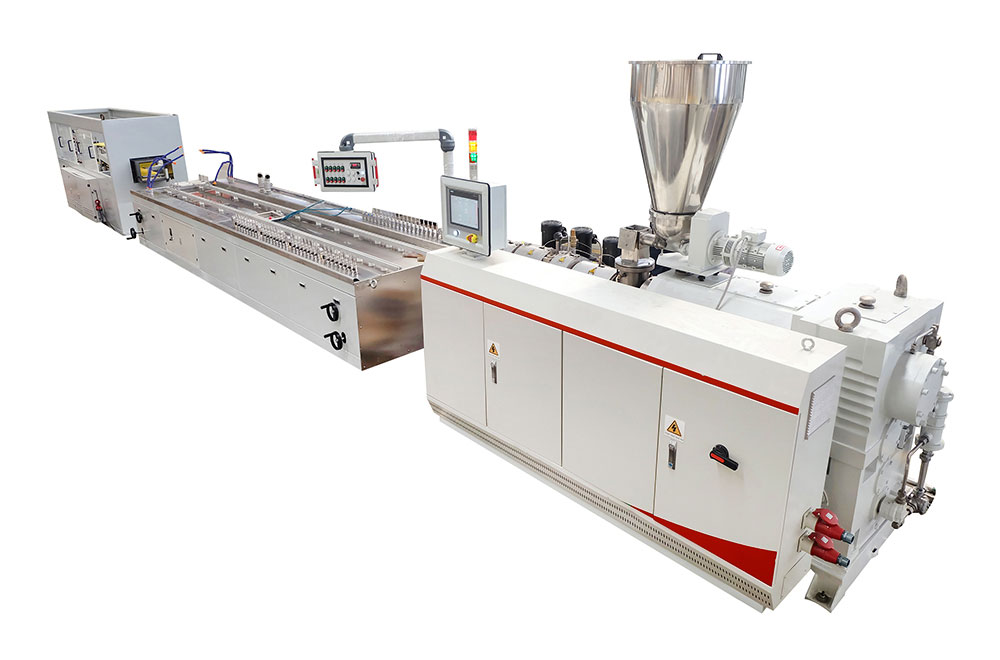
Situation Research: Successful Projects Utilizing Plastic Extrusion
Success stories in the field of plastic extrusion are plentiful, showing both the versatility and performance of this manufacturing procedure. plastic extrusion. Another effective situation is the production of plastic movie for packaging and farming. These circumstances illustrate plastic extrusion's vital duty in different industries, proving to its flexibility, cost-effectiveness, and dependable output.
Conclusion
In final thought, plastic extrusion provides a affordable and reliable approach for generating complex shapes with minimal waste. Integrating plastic extrusion right into tasks can lead to successful end results, as shown by various instance studies.
Plastic extrusion, a staple in the production industry, is a procedure that includes melting raw plastic product and reshaping it right into a constant profile. Plastic extrusion can take care of a range of plastic Click This Link types, expanding its application range.How can make constraints potentially affect the procedure of plastic extrusion? The procedure of plastic extrusion entails melting plastic products, possibly releasing dangerous gases into the atmosphere. Utilizing recycled plastic products in the extrusion procedure can reduce environmental impact.
Report this page